|
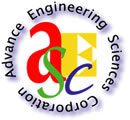 |
|
Delivering Advanced Engineering Solutions |
|
|
|
|
|
AESC has been an active participant in the growing approach to incorporate failure mode and effects analysis (FMEA) into the facility design. Use of FMEA has helped anticipate, identify and improve designs to avoid risks and failures before implementation. This approach has helped engineers to build safety into the design of the facility. The end product is facility that promotes safety for personnel, visiting clients, and occupants in general.
FMEA is at the heart of AESC's approach to facilities risk assessment. The process of conducting an FMEA requires a team made up of facility designers, intended use experts, and operations personnel that all participate in identifying "what could go wrong" with the intended use and processes. The results are then used by facility designers to eliminate those risks.
Following high level steps are part of AESC's approach to conducting a facility FMEA:
|
|
| Define the topic of the facility FMEA along with a clear definition of the systems and or processes to be studied. Note that this may lead to several independent FMEA studies that may be ultimately merged into an overall high level FMEA.
|
|
|
| The expert panel is made up of facility designers and subsystem experts. Typically this includes designers, subsystem engineers, operations, and maintenance team members. Panel members will be responsible for providing details regarding design, operation, and maintenance of the facility. They will also be responsible for review of FMEA studies to insure accuracy.
|
|
Process and Functional Description |
|
| Develop and verify chronological flow diagrams that describe processes, or equipment functions.
|
|
| Identified processes, or functions are indexed. |
|
| Identify all sub-processes, sub-functions |
|
| Develop flow diagrams for all sub-processes, sub-functions |
|
|
| List all potential failure modes under the sub-processes, sub-functions
|
|
| Determine the severity and probability of the potential failure modes
|
|
| Use facility FMEA decision tree (figure 2) to determine if the failure mode warrants further action
|
|
| Document all causes for each failure mode
|
|
|
| Decide if a failure mode can be eliminated, controlled, or accepted.
|
|
| Describe action(s) for each failure mode that will be eliminated or controlled. Elimination and or control of a failure mode may require redesign and requires responsible experts recommendation.
|
|
| Identify measures to analyze and test the "controlled" or redesigned process, function
|
|
| Identify and assign responsibility for completing the recommended action. |
|
| Obtain management's concurrence on the recommended actions. |
|
|
The FMEA process will also include quantification of risk which is based on the simple formula, Risk = Occurrence X Severity. The occurrence and severity are further categorized as per the following tables.
|
Table A: Occurrence probability Ranking
|
Rank |
Description |
Score |
Remote |
Unlikely to occur within service life |
1 |
Uncommon |
Possible to occur within service life |
2 |
Occasional |
Occurrence within service life is likely |
3 |
Frequent |
Several occurrences likely within service life |
4 |
Certain |
Frequent occurrences within service life |
5 |
|
Table B: Nominal Severity Ranking
|
Severity |
Severity Description |
Score |
Minor |
Loss of data without loss of functionality |
1 |
Moderate |
Loss of redundancy (without loss of operations) |
2 |
High |
Operation Interruption |
3 |
Major |
Possible personnel injury, possible environment risk |
4 |
Catastrophic |
Possible fatality, Environmental Risk |
5 |
|
In order to insure elimination of risk, the FMEA process including the quantification phase continues according to the following decision tree.
|
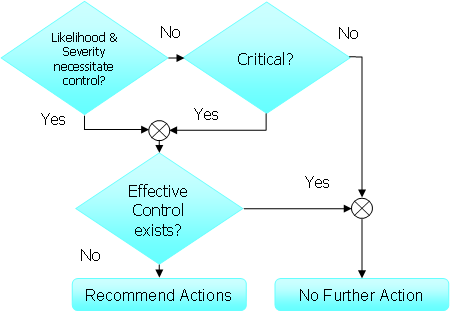 |
Figure 2 - Facility FMEA Decision Tree
|
|
|
|
|
|
|